Check out our Portfolio
What have we done for others? Take a look. It’s literally all over the map, in terms of industry and configurations.
Industrial IoT

Aerospace

Healthcare

Construction Equipment

Transportation

Consumer Goods/Retail

Oil and Gas

Consumer Safety

Industrial IoT
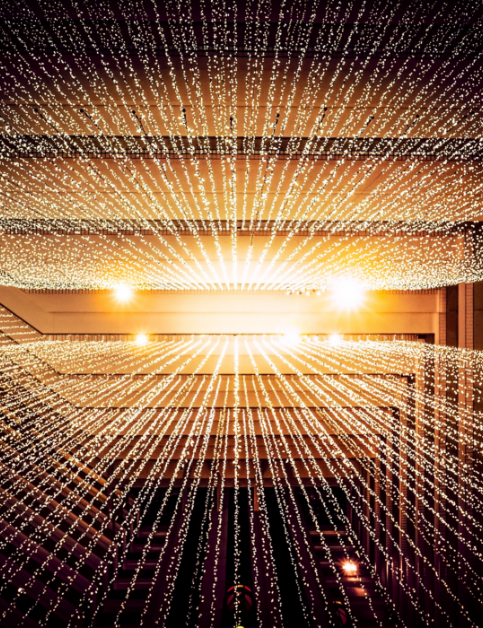
Situation:
A company that manufactures an ozone-based sanitizer for the water used in commercial ice makers wanted to increase its reach in the quick-service restaurant industry, its target market. While they knew their product was important to each restaurant’s operations, they didn’t have a way to alert restaurant owners when the sanitation cartridge should be replaced. Recommending replacement every few months wasn’t optimal, as many businesses are seasonal and usage varies accordingly. They needed a way to capture data so they could measure the sanitation levels on the ice makers, so they could take appropriate action when a sanitizer cartridge needed replacing.
Results:
We partnered with them to add an IoT component to the sanitation apparatus and connected the device to the cloud. Restaurant owners are now able to monitor usage conveniently. The owners receive an alert when it’s time to replace the sanitizer cartridge. Owners can view this and other usage data via an app, and can reorder cartridges directly from the app. They can also use the data to set proper cleaning schedules. The addition of an IoT connection helps restaurant owners run a more efficient and clean operation, increasing revenue for the consumable portion of the product.
Situation:
An industrial control company was looking to speed up their Research & Development process. They needed best-practice advice in wireless communications. The environmental requirements of the project were challenging due to the industrial setting; the devices would be installed in hard-to-reach places within hazardous environments. One particularly challenging requirement that arose was for extremely long battery life. Many years of battery life were required for each device to reduce the need for a tech to enter the environment for service. The technology they were working on would be used across multiple products, all of which were related to process control in industrial systems.
Results:
Our team joined their team and sped up the R&D process with our wireless communications expertise. We built prototypes, and conducted proof-of-concept tests that mimicked the environmental conditions in which the system will be deployed. We shared feedback with their R&D team, speeding up the overall design and development process. The relationship is still ongoing, and we are working closely with the company to continue to improve their technology at a rapid pace.
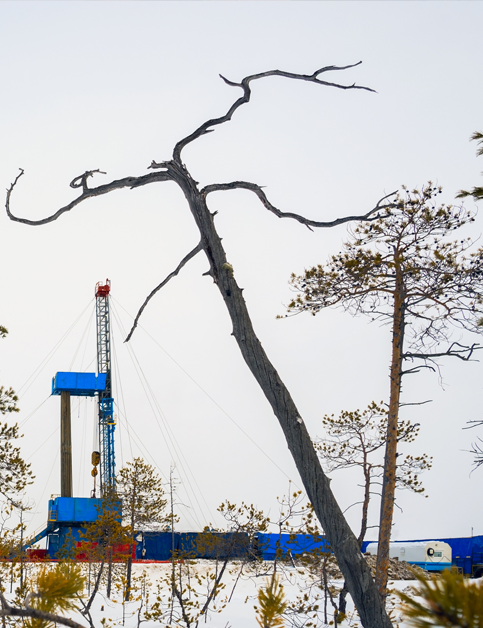
Healthcare
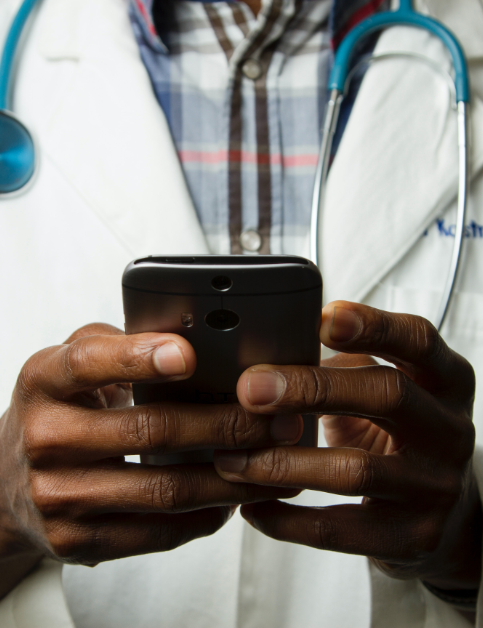
Situation:
A medical device manufacturer was concerned about data security and privacy. On many intelligent medical devices, there are a number of security considerations to be addressed. The physical machine itself must be secure, data the machine captures must be secure at rest and in transit, and the device must comply with HIPAA regulations. They couldn’t risk the hefty fines and reputational damage that come with HIPAA violations or—much worse—a successful attack on an insecure device. They didn’t have the embedded systems and IoT security expertise on their internal team to address these issues, so they came to us for best-practice guidance.
Results:
Our embedded cybersecurity team made recommendations regarding the system architecture to make sure the physical device and data are secure and adhere to industry regulations. We also assisted in creating a platform for automated testing of the medical devices, which sped up the testing process and improved the overall quality of the product. Our involvement enabled their in-house staff to focus their energy where they could add the most value—developing other products to bring to market—without having to worry about the often-overlooked yet crucial aspect of security in IoT devices and applications.
Situation:
A healthcare company needed to build automated software tests for their existing software. While their in-house engineers were capable of performing this work, it’s not their preferred type of project. They would rather focus on development, not testing. Additionally, testing your own software is never optimal; it can leave you open to missing issues because you’re simply just too close to it. A fresh set of eyes is more likely to identify problems. The company came to SDS to build and integrate automated software tests so that the testing process would not impinge on—or require—the work of their developers.
Results:
We have many team members who thrive on building automated software tests. Since we didn’t have first-hand knowledge of our client’s software coming into the project, we were also able to provide the fresh eyes needed to make sure testing was comprehensive in coverage, and that the code itself was built to be testable. We identified several issues with the software, which were fixed prior to it going into production. Since this software is used across multiple medical devices, remediating issues prior to production is critical for patient safety and costs. It is far less expensive to bring on consultants for thorough analysis and testing during development than it is to conduct a recall to correct issues in software that has already been deployed.
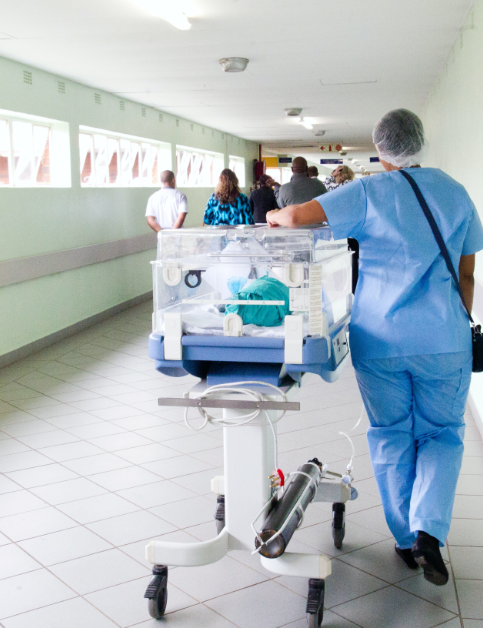
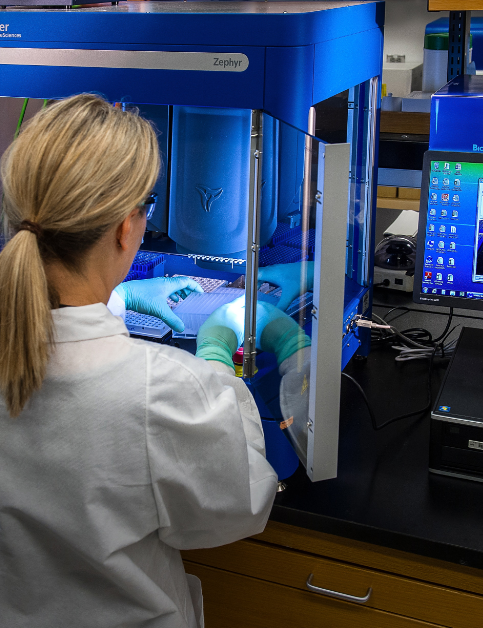
Situation:
A medical device manufacturer was building a vest that serves as a defibrillator for patients waiting for a pacemaker. There were a number of tasks involved in the project that required embedded systems knowledge, including configuring an embedded Linux system for use in such a critical application.
Results:
The company brought us in specifically for the embedded systems work. Their team was able to focus on their domain of expertise—critical medical devices—and we focused on our area of specialty. This type of project is ideal for embedded systems consultants, as we can come up to speed quickly and provide the necessary knowledge. Their team was able to continue to work and meet deadlines, without being slowed down by tasks outside of their domain. Having people in our own families who have used this defibrillator vest while waiting for implantable defibrillator surgery provided a special bond with this project, and we were proud to be a part of it.

Transportation
Situation:
A railway systems manufacturer had a wide range of testing equipment for manufacturing, production, and repair. Each type of testing equipment had varying levels of automation built in, ranging from zero to moderate automation. The equipment was aging and didn’t have a friendly or updated user interface. They could no longer maintain the outdated equipment. It was time for an upgrade.
Results:
We paired one of our skilled engineers with one of their domain experts to build the next generation of automated testing equipment (ATE). We focused first on ATE to streamline repairs, and then moved on to updating and digitizing their manufacturing processes. We are now incorporating predictive analytics, using the Internet of Things, by sending in live data from units in the field back to the depot for analysis. The new automated approach reduces costs, is more reliable, and is easily repeatable.
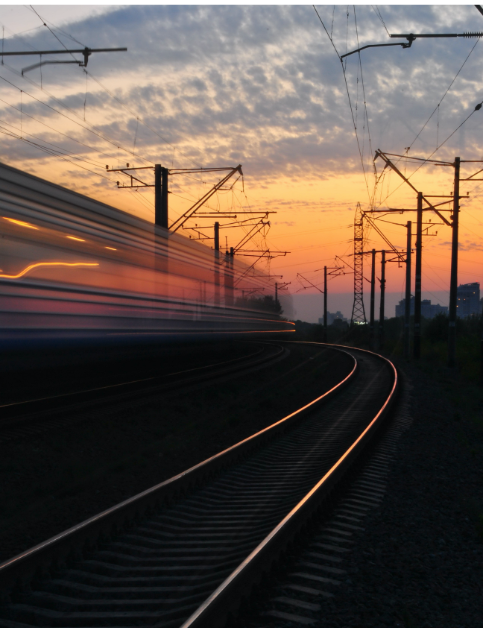

Oil and Gas
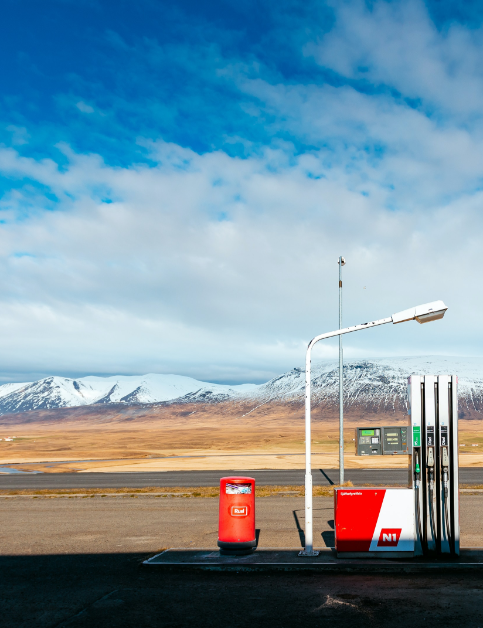
Situation:
A global leader in oil and gas, this company uses its proprietary technologies and production systems to bring innovation to midstream and downstream oil and gas projects. They manufacture meters, valves, and pumps used for onshore and offshore drilling, pipelines, and distribution systems. One specific product they were looking to modernize was the metering system used to fill tanker trucks that deliver gasoline to gas stations. Because the oil and gas industry is highly regulated by the National Institute of Standards and Technology (NIST), these regulations had to be factored into the solution. When a tanker pulls into a depot for refueling, it needs to load specific amounts of regular, premium, and diesel fuel. The driver must be verified as legitimate, and the purchase order must also be verified for the various types and quantities of fuel. They needed a modern-looking solution that would optimize the driver’s experience, automate the metering and measurement process, and be compliant with industry regulations.
Results:
The embedded systems experts on our team partnered with their metering experts to build a high-performing embedded system with a touchscreen user interface, replacing the outdated metering system. Our team worked on the system architecture, was involved in the decision-making process around architecture design, and built the system to meet the performance and compliance requirements. The new meters are easier to operate, capture valuable data, and keep the company compliant with NIST regulations.
Situation:
A manufacturer of lubrication systems for compressors in the oil and gas industry developed a new lubrication product that drastically reduces the amount of lubrication needed for the compressors. Their current measuring system, however, wasn’t equipped to provide the extremely precise lubrication measurements needed for the new product. They developed a prototype of a new system that could measure the product in minute increments, but didn’t have the in-house expertise or resources to complete the prototype and execute the design.
Results:
We partnered with them to complete the prototype. Together, we designed and developed an embedded system to precisely measure the lubrication amounts. We also developed a cloud-based application to capture the data and manage the devices, and integrated it with their order management system. Embedded sensors now monitor the level of lubricant and send an alert when it is getting close to needing a refill. The company can now offer automated fulfillment and can ship small, precise quantities of their product via UPS rather than sending out a giant tanker truck for a refill. This is a total game changer for this company and this process.
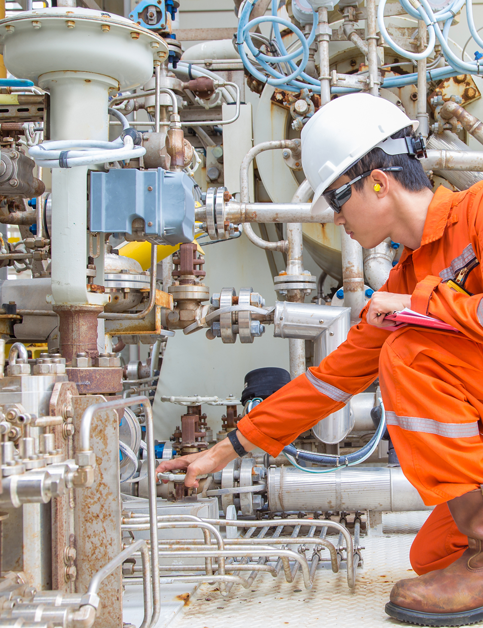

Aerospace
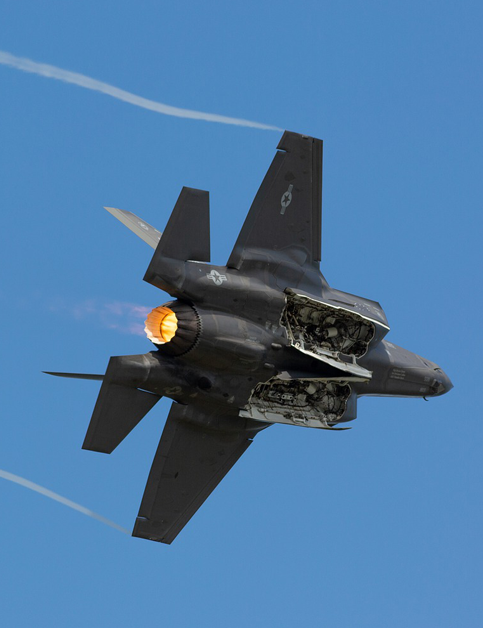
Situation:
A defense contractor manufactures a critical optics component of the F-35 Joint Strike Fighters for the Department of Defense (DoD). The DoD directed that this enormously complex aircraft must be maintainable in the field, rather than requiring components to be shipped back to the original manufacturer for repair. The main challenge in this case was that the manufacturer is staffed by trained experts, while the airbase is staffed by field technicians with much less training. Additionally, the fighter’s optical component built by our client is highly complex and would be extremely challenging to repair without prior experience and extensive training.
Results:
Our domain experts worked with their domain experts to build automated testing software that automatically scans all of the components of the system and analyzes the results. If something is wrong, the software carefully leads the technician through diagnosis and repair, including repair of the complex optical component. The software then retests the component to confirm it is working properly after repairs are made. This ensures that only working components are put back on the fighter. We have built several other automated testing systems for this client, used for both field repair and for production line testing. These systems have increased the speed and accuracy of quality control in a cost-effective manner.
Situation:
A high-tech aeronautics company is building an uncrewed lander that will be deployed to the moon in 2021. The lander will deliver a variety of payloads from several sources to the lunar surface to conduct a range of scientific activities. As part of its spacecraft design, the company is creating a common framework for payload electronics, which includes extremely compact and complex circuit boards. They needed a mechanism for testing these boards consisting of a fixture to place the circuit boards in, which would also provide pathways for power and signals to test them prior to assembly and launch.
Results:
We are working side by side with the aeronautics company, putting our hardware, software, and mechanical engineering expertise to good use. We are building both the hardware and software required to individually test each circuit board prior to assembly and to conduct system-level testing. This is a particularly challenging project since the circuit boards are so complex and compact, using specialized components designed for the harsh environment of outer space. The fixture that holds them needs to be able to accept them easily and make them readily accessible for testing and debugging. Our expertise in system testing allowed us to identify suitable substitutes for costly space-qualified components usable for ground testing, an important workaround to meet testing requirements and cost goals. We also have an engineer on staff with experience in military aerospace technologies, enabling us to add even more value to this exciting project.
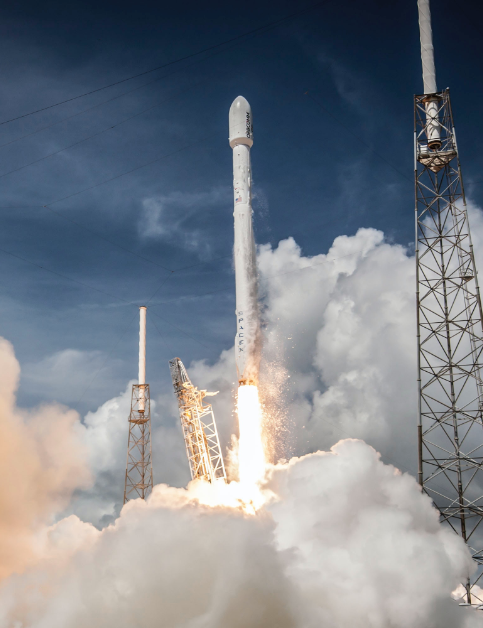
Construction Equipment
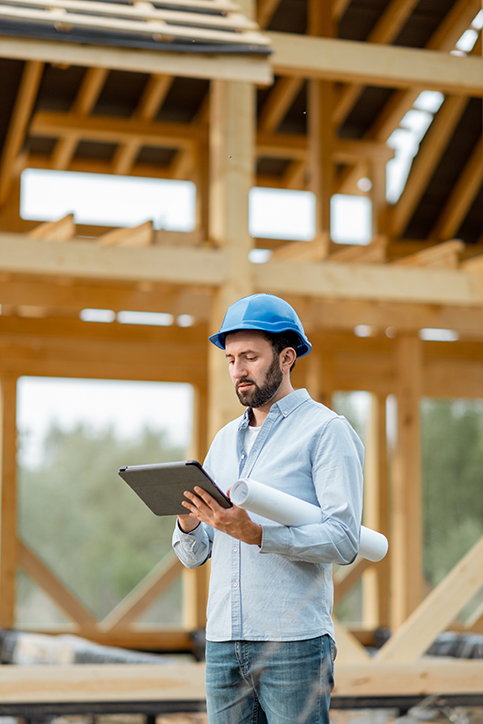
Situation:
A manufacturer of industrial-quality handheld pneumatic tools (nail guns, staple guns, etc.) sold largely to business-to-business customers in the construction industry, including large-scale housing and roofing professionals, small-shop upholstery makers, manufactured homes factories, and more. Nail guns haven’t changed much over the years, and the company wanted to develop a new innovation that would help them stand out in the marketplace. They considered the needs of their various customers when developing ideas, and expanded their thinking to include what is possible now that was not possible in the past. They knew that all of their customers care most about efficiency and safety, and they realized that the Internet of Things presented a new opportunity; namely, to capture data from their pneumatic tools, bring it to the cloud for analysis, and feed the data back to their customers. This would enable them to improve their usage, optimize their maintenance, and meet their goals.
Results:
We worked with the client to add embedded sensors to the pneumatic tools. We were able to capture data about how many times the tool was fired, how it was being held, the air pressure when it was fired, and how far it was being held from the target. These parameters influence maintenance, service and replacement schedules, and safety training. There were some limiting factors we had to account for in our design. For starters, the tools run on air rather than electricity, so every sensor had to be battery-powered. Minimizing power usage to optimize battery life became a primary goal. The tools are also used in harsh environments (outdoors, rain, mud) and are often thrown around on the job site, so our design had to withstand the harsh conditions (a classic scenario in Industrial IoT). We conducted several rounds of R&D and prototyping until we were able to balance functionality and cost. The company is now bringing change to its industry, and receiving increased attention at trade shows due to their innovation.
Consumer Goods/Retail
Situation:
A global leader in the application of conductive inks in the retail sector was designing “smart shelves” and “smart pegs” that would alert retail managers that stock was low, items were misplaced, or a theft may have occurred. The overall goal was to bring smart inventory management to physical retail stores. Both products require a complicated communications architecture, due to the variety of physical products to be tracked and the wireless technologies needed to send and receive data. The solution also needed to be low-latency and able to withstand the harsh environment of retail stores where customers and workers are constantly handling and moving inventory. The company had committed to demonstrating a working version of both products at an upcoming trade show, making deadlines tight, so they turned to SDS for help.
Results:
We designed and developed the software architecture for the entire system, as well as some of the firmware for the products. The new cloud-based system allows retailers to remotely set alerts, and log in from any location to monitor on-the-shelf inventory. Headquarters can check inventory counts at various locations, identify when products are moving in and out, and associate products moving off the shelf with the point-of-sale information that is captured. The system is able to withstand the harsh retail environment. It can be turned on and off repeatedly, and reconnects to the network automatically. It can use wireless communications within the store, or be wired to a single gateway. We also created a database to serve as a historical record of the product data. Retailers can use this actionable data for theft and out-of-stock prevention, planogram compliance, long-term stocking procedures, and to identify supply chain efficiencies and product trends. These efficiencies are helping brick-and-mortar retailers digitize their physical stores so they can better compete with the online giants.
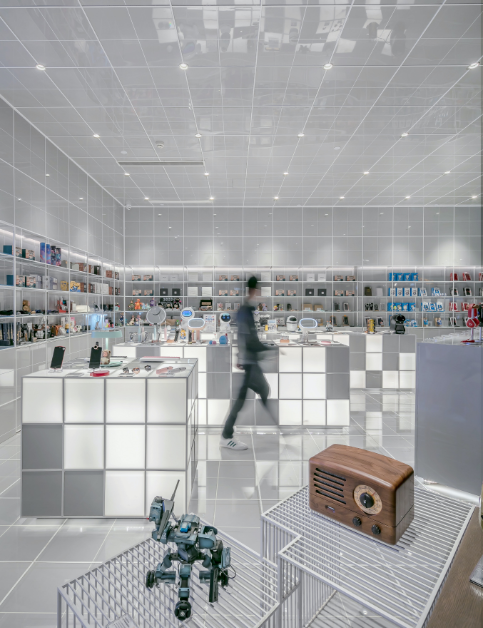
Consumer Safety
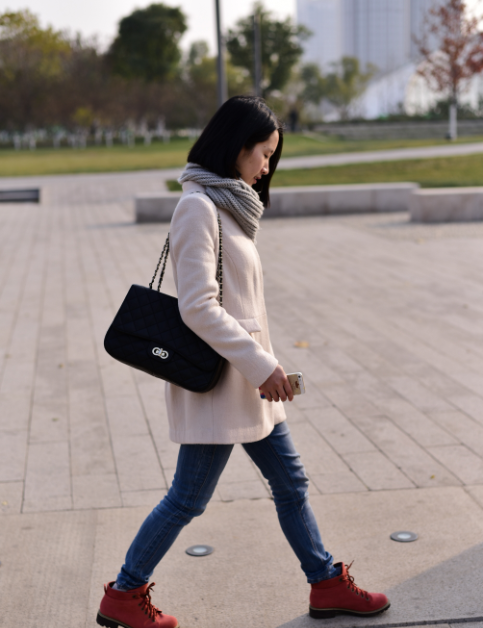
Situation:
A biotechnology company that focuses on personal safety products for women was leveraging the Internet of Things (IoT) to design a women’s safety device that can identify—from biometric parameters—when a woman is possibly in a dangerous situation. The goal is for the device to measure physiological parameters of the wearer and, through a machine learning algorithm, determine if those parameters indicate that the wearer is facing danger (sensing a “fight or flight” response for example). If so, the device uses the wearer’s cell phone, through a custom app, to communicate the wearer’s condition and location to her network of contacts. The company lacked the hardware expertise in-house to complete the design and development, so they partnered with SDS on the product.
Results:
We put our experience in embedded systems, hardware, and rapid prototyping to good use, working closely with their biotech team. The end result was an IoT device consisting of a wearable patch that measures skin response and heart rate, as well as tracking the wearer’s geographical location and other pertinent data. This information is sent to the user’s cellular phone via Bluetooth. An Android app on the user’s phone uses a machine-learning model to analyze the data and determine if the individual is in danger. If the algorithm determines a dangerous state is present, a call for help is sent to a predetermined support group for assistance. We worked together to enhance personal safety through IoT.