Automated Testing & Guided Repair
Complex and critical systems need advanced and/or automated testing; we’ve solved this problem numerous ways.We have spent years working on automated and semi-automated testing, helping clients create efficiency and reduce costs. We understand what is valuable to automate and what is not valuable to automate, because the truth is, some things are not ripe for automation.
It is critical to conduct proper testing prior to taking a product or system to production. The costs associated with recalls, reputational damage, and potential fines vastly outweigh the cost it takes to conduct proper testing during development. We have seen companies rush to fully automate processes, only to realize after the fact that certain steps are better performed manually. Time and money was lost both creating and undoing the automation process.
We have worked on countless projects automating processes for testing both physical components and software. Sometimes clients come to us looking for additional resources for automated testing. Their internal team may very well be capable of handling testing, but their time may be better spent focusing on development. Our team has years of experience in automated testing across various industries, making it simple for us to provide the additional resources needed to make sure your system is thoroughly and comprehensively tested.
Benefit of using external resources for testing
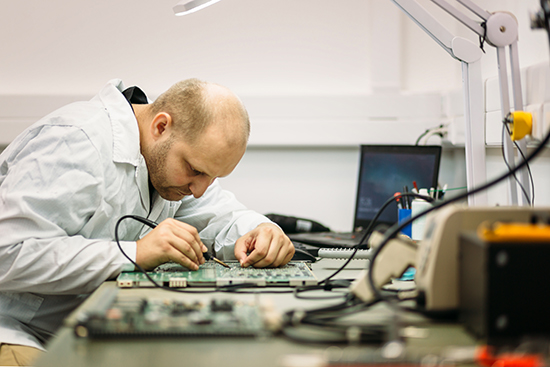
Experience across many industries
As an example, we recently worked on a project with a defense contractor on a project in which F-35 Joint Strike Fighters had to be maintained in the field by technicians. The fighter contained extremely complex optical components, increasing the difficulty for someone to repair it without prior experience or training.
We worked with the client to build automated software to scan all of the system components and analyze the results. If something is wrong, the software carefully leads the technician through diagnosis and repair, including repair of the complex optical component. The software then retests the component to confirm it is working properly after repairs are made. We have built several other automated testing systems for this client to increase the speed and accuracy of quality control in a cost-effective manner.
Regardless of your industry or domain, we have the knowledge and expertise to help you decide what tests to automate, how to automate them, and how to guide individuals through the repair process.
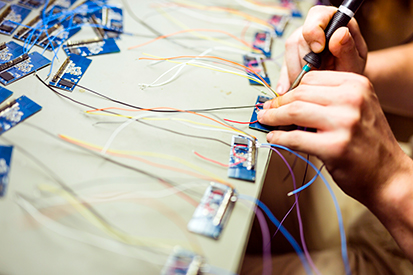